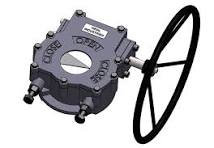
In industrial processes, automated valves play a critical role in controlling fluid flow, pressure, and temperature across systems. The automation of these valves requires precise and reliable actuation methods to ensure they perform as expected under diverse operational conditions. This is where gearboxes come in as essential components, enhancing the performance and durability of industrial valve automation. Gearboxes are integral to controlling large industrial valves, offering torque multiplication, improved control, and a reliable mechanical advantage. This article explores the various roles gearboxes play in industrial valve automation, their types, advantages, and key considerations for selection.
1. The Importance of Gearboxes in Industrial Valve Automation
Gearboxes provide the necessary torque to open and close industrial valves, which are often too large or operate under pressures too high to be manipulated manually or by direct motor drive alone. Gearboxes allow for smoother, more controlled operation by adjusting torque and speed to match the valve’s requirements. This is especially critical in large-scale applications found in oil and gas, water treatment, power generation, and chemical processing industries, where precision, reliability, and safety are paramount.
In essence, gearboxes serve two main functions in valve automation:
- Torque Amplification: They amplify the torque needed to actuate large or high-pressure valves.
- Speed Reduction: They slow down the input speed to allow more controlled, gradual opening and closing of valves, which is essential in preventing water hammer or other pressure surges.
2. Types of Gearboxes Used in Valve Automation
There are several types of gearboxes designed to cater to different valve automation needs. The choice of gearbox often depends on the valve type, system requirements, and operating conditions.
a. Bevel Gearboxes
Bevel gearboxes use bevel gears, which are conically shaped and meshed at right angles. They’re common in 90-degree turn valves like butterfly and ball valves. The key advantage of bevel gearboxes is their ability to handle high torque while maintaining a compact design. They are reliable and require minimal maintenance, making them suitable for applications where space and longevity are concerns.
b. Worm Gearboxes
Worm gearboxes consist of a worm (screw) and a worm gear, allowing for significant torque multiplication with a single input. Due to the high gear reduction ratio, worm gearboxes are ideal for valves that require a high torque but can operate at slower speeds. They’re often used in gate and globe valves. Additionally, worm gearboxes have a natural locking mechanism, preventing back-driving, which adds a level of safety in critical applications.
c. Spur Gearboxes
Spur gearboxes use straight-cut gears to transmit motion between parallel shafts. While they are simpler in design and typically less expensive, they are not as efficient at torque multiplication as bevel or worm gearboxes. However, spur gearboxes are suitable for applications requiring moderate torque, such as smaller ball and plug valves.
d. Planetary Gearboxes
Planetary gearboxes feature multiple gears arranged in a configuration that offers high torque density and compactness. They are increasingly popular in advanced valve automation systems due to their ability to deliver high torque in a relatively small package. This makes them suitable for high-pressure applications where space is limited.
3. Advantages of Gearboxes in Valve Automation
Using gearboxes in valve automation systems offers several advantages, enhancing both operational efficiency and safety. Here’s a closer look at these benefits:
a. Enhanced Control and Precision
By reducing the speed of the input motor and increasing torque, gearboxes enable precise control over valve movement. This is crucial in processes where fluid flow and pressure need to be finely tuned. For example, in chemical processing, even a slight deviation in flow rate can affect product quality.
b. Increased Safety and Reliability
Gearboxes contribute to system safety by offering a stable and reliable actuation method, especially in applications where pressure changes rapidly or is unpredictable. The torque multiplication capabilities prevent the motor from stalling and the gearbox’s ability to maintain a consistent speed can prevent water hammer and other pressure-related issues.
c. Energy Efficiency
With a gearbox, the motor driving the valve does not need to be as powerful, which conserves energy. By optimizing torque and speed, gearboxes reduce the load on the motor and decrease energy consumption over time, which is beneficial in systems that require continuous or frequent valve operations.
d. Reduced Wear and Tear
In applications where large valves are subjected to high stress, gearboxes distribute the load more evenly, minimizing the direct impact on valve components. This extends the lifespan of both the valve and the actuator, reducing maintenance needs and operational costs.
4. Key Considerations for Selecting Gearboxes in Valve Automation
When selecting a gearbox for valve automation, several factors come into play to ensure compatibility and efficiency. Here are a few critical aspects to consider:
a. Torque Requirements
Understanding the torque demands of the valve is fundamental to choosing the right gearbox. The gearbox should provide sufficient torque to operate the valve smoothly without straining the actuator or motor. Calculating the valve torque requirements based on the operating conditions—such as fluid pressure and flow—is essential.
b. Speed Requirements
Different industrial processes require valves to open and close at varying speeds. A gearbox with the appropriate reduction ratio ensures the valve operates at the desired speed without risking pressure spikes or system instability. For example, fast-opening valves in emergency situations may need a different gearbox configuration than those in gradual, continuous processes.
c. Environmental Conditions
Industrial environments can expose gearboxes to harsh conditions, such as high temperatures, moisture, dust, and corrosive chemicals. Therefore, it’s vital to choose gearboxes made from materials that resist corrosion and withstand the environment they will be exposed to. Additional coatings or sealing can enhance durability in extreme environments.
d. Compatibility with Actuators
Not all gearboxes are compatible with every actuator type. Compatibility between the gearbox and the actuator is essential to ensure the system functions as intended. Checking specifications for compatibility with electric, pneumatic, or hydraulic actuators is crucial during the selection process.
e. Maintenance and Accessibility
Selecting a gearbox that requires minimal maintenance and can be easily accessed for repairs or inspections is beneficial for reducing operational downtime. Gearboxes that are easy to inspect and maintain often have a longer service life, as regular checks can prevent minor issues from escalating into major failures.
5. Future Trends in Gearbox Technology for Valve Automation
As industries evolve, so do the requirements for valve automation systems. Gearboxes are increasingly integrated with advanced control systems, allowing for real-time monitoring, diagnostics, and predictive maintenance. Additionally, as industries push for more sustainable solutions, gearboxes are being developed to enhance energy efficiency and reduce environmental impact. Advances in materials science are also leading to lighter, more durable gearboxes capable of handling even higher pressures and torques.
Conclusion
In the world of industrial valve automation, gearboxes play a vital role in ensuring that valves operate efficiently, reliably, and safely. By amplifying torque, reducing speed, and enhancing control, gearboxes allow for precise valve operation, making them indispensable in applications where reliability is non-negotiable. Selecting the right gearbox involves careful consideration of factors like torque, speed, and environmental conditions to ensure long-term performance and minimal maintenance. As technology continues to advance, gearboxes will become even more integral to achieving efficient and sustainable industrial automation solutions.