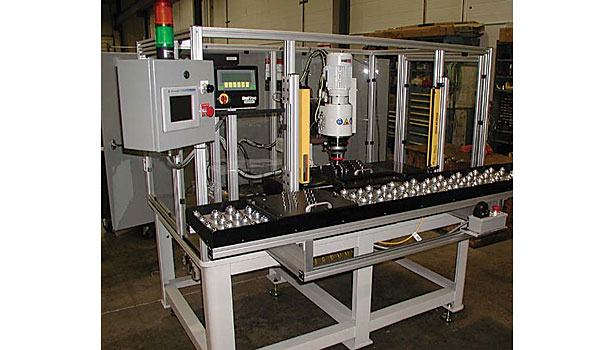
If you’re involved in manufacturing, you know how critical the assembly process is. Riveting, a popular joining method, requires precision, speed, and consistency. That’s where the automated riveting machine comes in. By automating riveting, manufacturers gain efficiency and quality that manual riveting just can’t match.
Want to learn more about how these machines can transform your line? Check out this Automated Riveting Machine solution for expert insights and services.
Now, let’s dig into the many benefits automated riveting machines bring to the table.
What Is an Automated Riveting Machine?
An automated riveting machine is a piece of industrial equipment designed to join materials — usually metal sheets or components — by driving rivets automatically. Unlike manual riveting, these machines use robotic arms or precise mechanisms to position, insert, and secure rivets rapidly and consistently.
They’re widely used in automotive, aerospace, electronics, and heavy machinery manufacturing.
Why Manufacturers Are Switching to Automated Riveting
Manual riveting can be time-consuming and prone to human error. Automated riveting machines solve these problems by:
-
Increasing production speed without sacrificing quality
-
Ensuring uniform rivet placement and force
-
Reducing operator fatigue and injury risks
-
Lowering scrap and rework rates
This makes automated riveting an attractive choice for any high-volume or precision assembly line.
Key Benefits of Automated Riveting Machines
Let’s break down the core advantages:
1. Enhanced Productivity
Automated riveting machines operate continuously and faster than humans, significantly increasing throughput. They can work on multiple parts in sequence or even simultaneously in advanced setups.
2. Superior Consistency and Quality
Because the machine applies exact pressure and placement, every rivet is uniform. This reduces the risk of weak joints or defects that compromise product reliability.
3. Improved Worker Safety
Riveting manually often exposes workers to repetitive strain injuries or accidental pinching. Automation removes humans from these risks by handling the physical tasks.
4. Cost Efficiency
Though initial investment might be substantial, automated riveting lowers labor costs and minimizes costly errors or scrap, offering a strong return on investment.
5. Flexibility and Adaptability
Modern machines can be programmed for different rivet sizes and materials, making them suitable for various products and production lines.
How Automated Riveting Machines Work
The operation typically follows these steps:
-
The machine receives parts either manually or via a conveyor system.
-
A robotic arm or mechanism aligns the rivet with the hole.
-
The riveting tool applies the precise force to secure the rivet.
-
Sensors confirm proper installation before the part moves forward.
This cycle repeats rapidly with little downtime.
Industries Benefiting from Automated Riveting
Industry | Typical Applications |
---|---|
Automotive | Body panels, chassis assembly |
Aerospace | Aircraft skin panels, structural joints |
Electronics | Enclosures, device assembly |
Heavy Machinery | Frame construction, equipment assembly |
Consumer Appliances | Metal casing and internal frame joining |
Automated riveting machines suit any industry needing strong, consistent joints at scale.
Automation vs. Manual Riveting: What’s the Difference?
Feature | Manual Riveting | Automated Riveting |
---|---|---|
Speed | Limited by human operator | Much faster with continuous operation |
Accuracy | Prone to variation and human error | High precision with consistent force |
Worker Safety | Potential strain and injury | Significantly safer |
Cost | Lower initial cost, higher labor cost | Higher initial cost, lower operating cost |
Quality Control | Manual inspection required | Integrated sensor feedback |
Automated riveting clearly offers more efficiency and consistency.
Choosing the Right Automated Riveting Machine
When picking a machine, consider:
-
Production volume and speed requirements
-
Types and sizes of rivets used
-
Integration with your existing production line
-
Ease of programming and operator training
-
Availability of after-sales support and maintenance
Consulting experts in automated riveting machine services ensures you get the right fit for your needs.
Maintenance Tips for Automated Riveting Machines
Keeping your machine in top shape is key to maximizing ROI:
-
Regularly clean rivet feeders and tools to prevent jams
-
Lubricate moving parts per manufacturer recommendations
-
Perform periodic calibration to maintain riveting force accuracy
-
Train operators on troubleshooting and basic maintenance
-
Schedule professional servicing annually
Proper maintenance avoids unexpected downtime and costly repairs.
Future Trends in Automated Riveting Technology
Automation technology continues to advance. Look out for:
-
AI and machine learning integration for predictive maintenance and quality optimization
-
Collaborative riveting robots working safely alongside humans
-
Vision systems for enhanced quality inspection in real-time
-
Lightweight, portable riveting robots for flexible manufacturing setups
Staying updated helps manufacturers maintain a competitive edge.
Final Thoughts: Is Automated Riveting Right for You?
If your business demands speed, quality, and scalability in assembly, automated riveting machines are a game changer. They boost productivity, improve safety, and reduce costs, making them a smart investment for manufacturers.
Want to explore customized options? Reach out to the Automated Riveting Machine specialists to see how automation can enhance your production line.