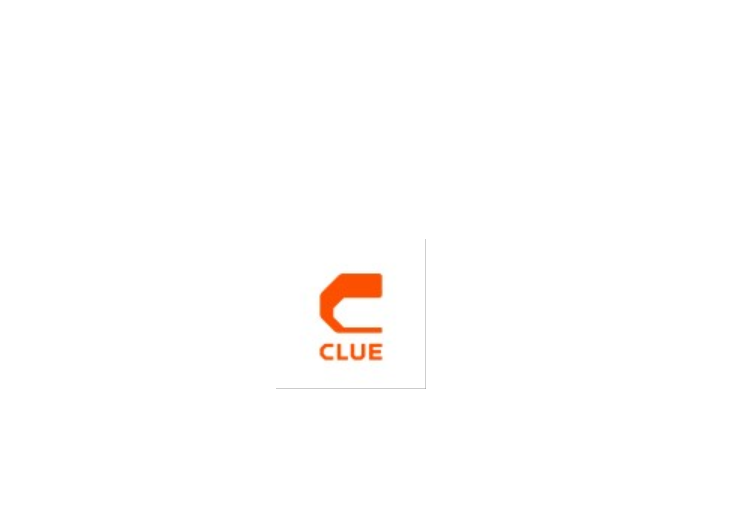
In construction, your machines are your moneymakers. When they’re running, projects stay on track. When they’re down, everything grinds to a halt, literally.
That’s why construction equipment maintenance software has become a mission-critical tool for modern contractors. It’s not just about fixing problems; it’s about preventing them altogether.
As fleets grow and job sites spread across multiple locations, manually tracking service schedules just doesn’t cut it anymore. The companies winning in this high-stakes game are those using smart scheduling tools to plan, predict, and stay ahead of breakdowns.
What’s Broken with Traditional Maintenance Methods?
Most companies still treat maintenance like a reaction, not a strategy. They wait for something to go wrong, then scramble to fix it—often at the worst possible time. That approach leads to:
-
Unplanned downtime
-
Costly emergency repairs
-
Safety hazards
-
Shortened equipment lifespan
According to a 2023 report by Equipment World, reactive maintenance can cost up to three times more than planned maintenance. Multiply that across a fleet of 50+ machines, and you’re bleeding money you don’t need to.
Worse yet, manual scheduling using Excel, whiteboards, or sticky notes—is prone to human error. Missed inspections, delayed oil changes, or forgotten part replacements all add up fast.
Why Maintenance Scheduling Software Is a Game-Changer
Maintenance isn’t just a wrench-and-oil job anymore. It’s a data-driven strategy. And software is the secret weapon that makes it all work.
1. Prevent Downtime Before It Happens
With construction equipment maintenance software, you can schedule service intervals based on real-time data—like engine hours, mileage, or usage cycles. No more guesswork. Just precise, automated triggers.
The result? Equipment gets the attention it needs before it breaks down.
A 2024 survey by The Association of Equipment Management Professionals (AEMP) found that companies using scheduling software reduced unscheduled downtime by up to 40%.
2. Centralized Maintenance Records
Every inspection, oil change, and repair is logged in one place—digitally. Whether you’re in the office or onsite, you have instant access to machine histories, upcoming services, and technician notes.
This isn’t just good practice. It’s also gold during audits, warranty claims, and insurance reviews.
3. Improve Fleet Lifespan and Performance
Well-maintained equipment lasts longer and performs better. It’s that simple.
Using automated reminders and service calendars, companies can extend the usable life of their assets, delay costly replacements, and ensure machinery runs at peak efficiency.
One case study by Fleetio showed a contractor who extended their equipment lifespan by an average of 18 months just by following a digital maintenance schedule.
4. Save Time and Reduce Administrative Overhead
Let’s be honest—maintenance paperwork sucks. Scheduling software removes the need for back-and-forth calls, calendar checks, or manual log entries.
Technicians can receive alerts, input service data on the go, and close out tasks with a few taps. The whole process becomes lean, fast, and scalable.
With tools like Clue, teams can automate scheduling, log service reports on the go, and maintain a fully digital maintenance history. Its maintenance scheduling is simple, scalable, and smart.
Looking Ahead: The Smart Future of Maintenance
What’s coming next? Even smarter tools.
AI and IoT integrations are turning construction equipment maintenance software into fully predictive systems. Sensors on machines now feed live data back into the platform, which uses algorithms to flag issues before they even become visible.
Expect these trends to take over:
-
Predictive analytics: AI models that recommend when to service based on usage and wear patterns.
-
Connected equipment: Machines that alert you directly when maintenance is needed.
-
Automated parts ordering: Software that syncs with vendors to auto-order filters, fluids, and parts ahead of time.
By 2027, the global market for predictive maintenance software is expected to surpass $23 billion, according to MarketsandMarkets. That’s not just a shift—it’s a full-blown evolution.
Conclusion
Let’s be blunt, reactive maintenance is a silent killer in construction. It burns budgets, stresses crews, and wrecks timelines. Construction equipment maintenance software flips that script by giving you control, foresight, and peace of mind.
If you’re still relying on spreadsheets and crossed fingers to manage your fleet’s health, you’re falling behind. The future belongs to those who treat maintenance as a strategic advantage, not just a chore.