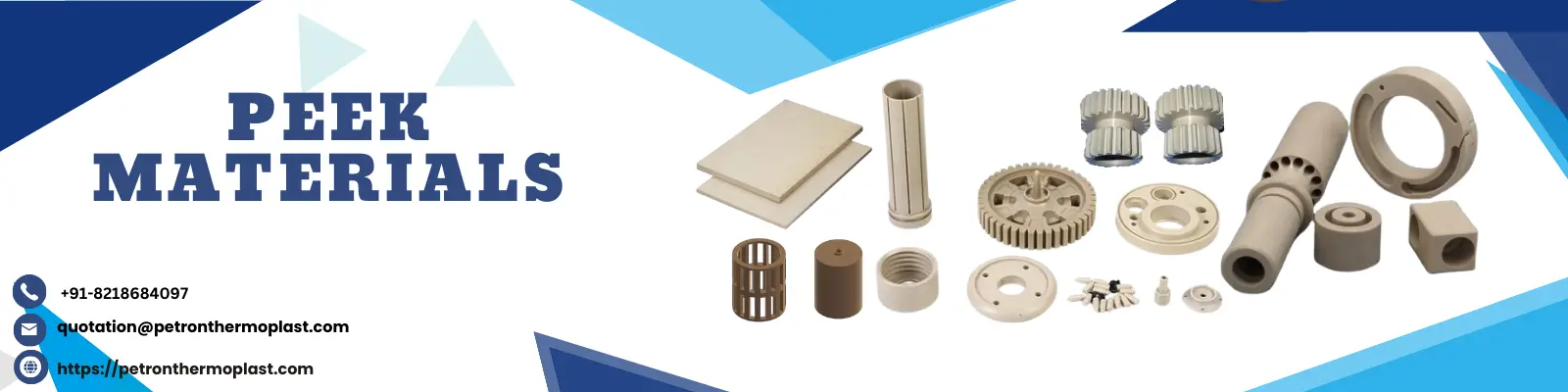
When it comes to high-performance plastics, PEEK material (Polyether Ether Ketone) stands out as one of the most advanced and versatile engineering thermoplastics available today. Its exceptional properties have made it a go-to choice for industries that demand strength, precision, and resistance to extreme conditions. Whether you’re in aerospace, medical, automotive, or electronics, understanding the benefits of PEEK can transform how you approach engineering and product development.
What is PEEK?
PEEK is a semi-crystalline thermoplastic known for its outstanding mechanical strength, chemical resistance, and thermal stability. Developed in the late 20th century, it quickly became popular for applications where metals and lower-grade plastics fail. PEEK offers a unique combination of performance and processability, making it ideal for critical components and demanding environments.
Key Properties of PEEK Material
-
High Temperature Resistance: PEEK can operate continuously at temperatures up to 250°C (482°F) and withstand short-term exposure to even higher temperatures without degrading.
-
Chemical Resistance: It is resistant to a wide range of aggressive chemicals, including acids, bases, and solvents, making it suitable for harsh industrial environments.
-
Mechanical Strength: PEEK offers high tensile strength and rigidity, comparable to some metals, while being much lighter.
-
Wear and Friction: With excellent wear resistance and a low coefficient of friction, PEEK is ideal for sliding and rotating parts.
-
Radiation and Hydrolysis Resistance: It performs well in high-radiation environments and resists hydrolysis in high-pressure steam applications, making it a preferred material in medical and nuclear applications.
-
Electrical Properties: PEEK has good insulating properties and dielectric strength, supporting its use in electronics.
Applications of PEEK
-
Aerospace: Lightweight and strong, PEEK replaces metals in various structural and mechanical parts, helping reduce overall aircraft weight and fuel consumption.
-
Medical Devices: It is used in implants, surgical instruments, and sterilizable components due to its biocompatibility and resistance to sterilization processes.
-
Automotive: High-temperature components like engine parts, transmission components, and seals benefit from PEEK’s durability.
-
Electronics: PEEK is used in high-performance electrical connectors, insulators, and semiconductor equipment.
-
Oil & Gas: Its ability to withstand extreme pressure and corrosive substances makes it ideal for downhole and subsea components.
Why Choose PEEK?
PEEK is more expensive than many other plastics, but its longevity, reliability, and superior performance often make it more cost-effective over time. It enables engineers and designers to push the boundaries of what’s possible in extreme applications.
Conclusion
PEEK material is a powerful solution in the world of high-performance plastics, offering a rare combination of thermal, mechanical, and chemical resistance. As industries continue to demand materials that can perform under pressure, PEEK remains at the forefront of innovation. Whether you’re replacing metal components or enhancing your product’s performance, PEEK is an investment in quality and durability.
For more insights into high-performance plastics and innovative materials, Petronthermoplast visit The Insider’s Views on Plastics and Polymers.