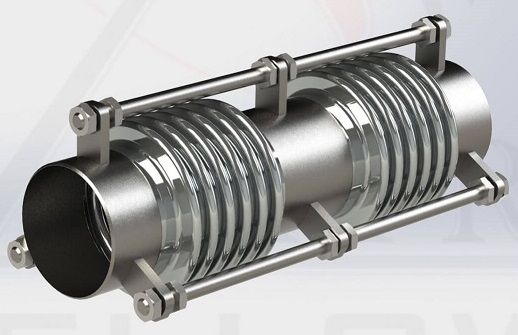
The current industrial advancement requires three essential core attributes: efficiency, durability, and safety. Every power plant, chemical facility, HVAC system, and marine application requires more resilient pipe systems due to the need for flexible capabilities in modern times.
The focal point within these systems is bellows expansion joints. These critical elements regulate thermal expansion and provide vibration attenuation and misalignment correction for pipelines.
What Are Bellows Expansion Joints?
The pipe work protection mechanism of Bellows expansion joints functions to absorb motions caused by thermal growth, pressure fluctuations, and mechanical oscillations. The component, made of stainless steel or alloy, serves as the bellows, which features multi-directional flexibility to protect the overall pipeline structure.
Among the expansion joints available for sale, bellows expansion joints excel because they support extreme pressure and heat conditions. Diverse operational settings within oil and gas, as well as power production facilities, chemical production, and water treatment facilities utilize expansion joints. Optimal piping system results depend on using both sealed expansion joints and flexible rubber expansion joints, depending on system requirements.
Emergency Response for Bellows Expansion Joint Failures
The total breakdown of operational processes becomes feasible due to abnormal equipment failures, which create serious operational stoppages and significant financial losses. Bellows expansion joints fail to handle tears or breaks due to fatigue, corrosion, and improper installation. A support team with the needed expertise demonstrates significant importance when it takes responsive action in emergencies.
Emergency support services ensure:
- Urgent diagnostics, along with the resolution of critical issues, are available 24/7.
- Qualified professionals perform both site checks and damage evaluation of the equipment location.
- Rapid fabrication or replacement of damaged expansion joints.
- Emergency support services implement temporary sealing methods and alternative routing solutions to minimize operational interruptions.
The availability of an experienced service partner with inventory and technical knowledge about every type of expansion joint, from sealed to rubber models, will prevent ongoing interruptions.
Scheduled Maintenance: Prolonging Life and Enhancing Safety
Bellows expansion joints require scheduled maintenance as part of standard mechanical practice to prolong their operational effectiveness. Preventive maintenance extends the lifespan of the joint and lowers the probability of sudden failure, while ensuring complete compliance with industry standards.
Key maintenance practices include:
- Routine visual and dye penetrate examinations help identify the first indicators of fatigue or cracking in the system.
- Pressure tests assess a joint’s operational capabilities in terms of performance.
- The mechanics require cleaning alongside lubrication of their moving components (if such parts exist).
- A thorough evaluation should be conducted on support structures and alignment to determine their effect on material stress.
The implementation of sealed expansion joints, along with flexible rubber expansion joints, during maintenance operations will produce a leak-free pipeline that resists high vibration and chemical aggression.
Expert Installation: Ensuring Structural Integrity from Day One
The premature failure of bellows expansion joints can occur when professionals install them incorrectly, even with high-quality manufacturing. Proper alignment, alongside anchoring and system integration, becomes possible through professional installation, which creates conditions for long-term reliability.
Why professional installation matters:
- Assembly personnel must select appropriate joints by considering operational pressure levels, as well as temperature and movement parameters.
- The proper placement, alongside correct orientation, enables support of axial motions, as well as lateral and angular movements.
- Properly manufactured components receive installation through welding and bolting actions, which follow standard coding protocols.
- Testing the system during startup ensures its proper operation when a new installation is complete.
Expert care about material compatibility needs to be combined with chemical resistance analysis when working on projects that use sealed expansion joints or flexible rubber expansion joints. The experts guarantee that all system elements, including gaskets and flanges, as well as adjacent components, work effectively together.
Inspection Services: Staying Compliant and Operational
The requirement for periodic inspections stems from regulations that go beyond just safety standards. Maintaining your expansion joints below, along with related components, requires assessment services that serve essential purposes. These services help protect your investment during insurance needs and insurance audit activities, while providing preventive insights.
Inspection protocols include:
- Visual and non-destructive testing methods form part of standard field surveys.
- Thermal imaging and ultrasonic testing for internal damage assessment.
- A system exists for documenting procedure steps, along with compliance reporting, to show traceability.
- Recommendations for corrective actions or system upgrades.
Sealed expansion joints serve as safety barriers to stop dangerous substances from leaking into chemical processing areas. Thorough inspection practices ensure that the joints maintain their air tightness while complying with all safety regulations.
When dealing with HVAC and water systems, inspectors must check flexible rubber expansion joints for wear marks, as well as signs of delaminating or chemical attack, mainly when operating with corrosive materials in changing temperatures.
Tailored Solutions for Diverse Industries
One size doesn’t fit all. Plate-level service organizations create custom solutions below the expansion joint based on assessments of individual application requirements. The selection of expansion joints and their support system needs to align with the special functioning requirements of each system during design work or municipal water system refurbishment.
Industries served include:
- Industrial steam systems that operate under high pressure demand strong metallic bellows as a solution.
- The treatment of water systems works best with corrosion-resistant flexible rubber expansion joints.
- Sealed expansion joints in chemical processing offer total leak proof functionality.
- Marine and offshore – Saltwater-resistant designs for shipboard and offshore platforms.
- HVAC systems use flexible devices to achieve thermal and vibration control throughout building mechanical installations.
Why Choose Us for Bellows Expansion Joint Support?
The partnership with a company that delivers complete bellows expansion joint services provides you with a life-cycle solution beyond the standard product delivery, such as:
- Company engineers and designers create custom products for both new projects and retrofit projects.
- 24/7 emergency repair and fabrication services.
- Routine maintenance and inspection packages.
- Certified technicians and quality assurance across every stage.
- Inventory of metallic, rubber, and sealed expansion joints for rapid deployment.
The team recognizes that every product system encounters particular issues. We handle each project task with focused creativity and deep care giving, regardless of your need to manage hot pipelines or fragile chemical processing systems.
Conclusion
Complex industrial systems require bellows expansion joints as integral components. Proper installation, maintenance, and inspection practices enable bellows expansion joints to safeguard infrastructure from expensive damage, optimize operational performance, and protect all users. The complete support system for these flexible connectors delivers maximum potential through both emergency services and expert inspection and installation.