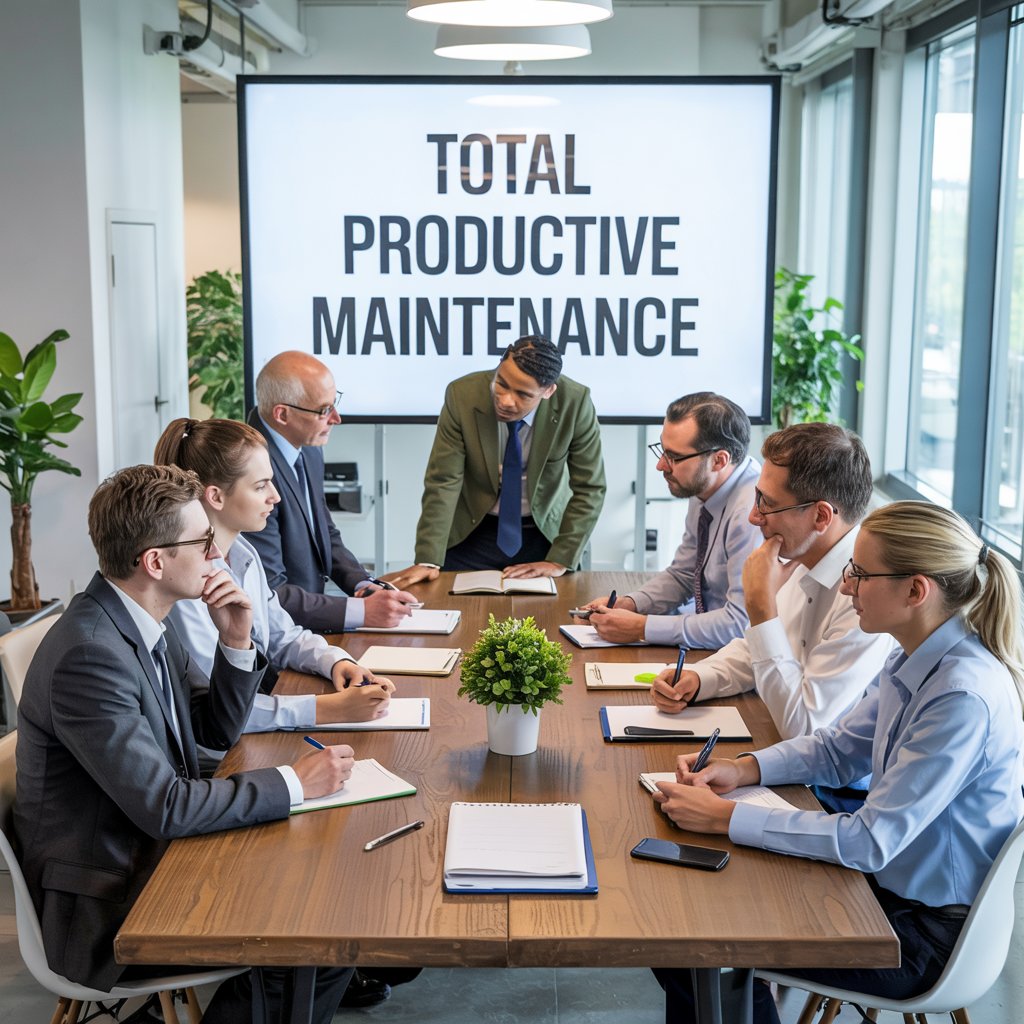
In the world of modern manufacturing and production, efficiency, quality, and reliability are the cornerstones of success. Equipment downtime, poor maintenance strategies, and reactive approaches to problems can cost organizations thousands—if not millions—of dollars each year. This is where Total Productive Maintenance (TPM) shines.
TPM is not just a maintenance methodology—it’s a comprehensive system that empowers companies to improve equipment reliability, involve all employees in the maintenance process, and foster a culture of continuous improvement. At Unichrone, we understand that getting started with TPM can feel overwhelming. That’s why we’ve created this step-by-step guide for beginners to help organizations implement TPM successfully from the ground up.
What is Total Productive Maintenance (TPM)?
TPM is a proactive maintenance approach that aims to maximize the effectiveness of equipment and machinery while promoting employee engagement. Unlike traditional maintenance models that assign all responsibility to the maintenance team, TPM involves everyone—from operators to top management—in maintaining and improving equipment performance.
The goal of TPM is to achieve:
- Zero equipment breakdowns
- Zero defects
- Zero accidents
- 100% equipment effectiveness
Step-by-Step Guide to Implementing TPM
Implementing TPM requires strategic planning, strong leadership, and consistent involvement from all employees. Here’s how to get started:
Step 1: Gain Management Commitment
Why it matters: Without leadership buy-in, TPM efforts may not get the support and resources needed for success.
How to do it:
- Present the benefits of TPM to top management.
- Align TPM goals with organizational objectives (e.g., reducing maintenance costs, improving OEE).
- Secure commitment for training, time, and budget.
Step 2: Create TPM Awareness Across the Organization
Why it matters: TPM is a company-wide initiative. Everyone needs to understand their role in the process.
How to do it:
- Organize TPM introduction workshops for employees at all levels.
- Share success stories and case studies from other companies.
- Communicate TPM objectives, benefits, and individual responsibilities.
Step 3: Establish a TPM Steering Committee
Why it matters: A dedicated team ensures structured implementation and progress tracking.
How to do it:
- Form a cross-functional team that includes members from production, maintenance, quality, and HR.
- Define clear roles, responsibilities, and performance metrics.
- Develop a TPM master plan with milestones and timelines.
Step 4: Select a Pilot Area
Why it matters: A pilot implementation helps you test, refine, and demonstrate the impact of TPM.
How to do it:
- Choose an area with frequent downtime or maintenance issues.
- Collect baseline data (OEE, breakdown frequency, quality defects).
- Identify improvement opportunities and engage employees in the pilot zone.
Step 5: Implement the 5S System
Why it matters: A clean, organized workspace is the foundation of TPM.
How to do it:
- Apply the 5S methodology: Sort, Set in Order, Shine, Standardize, Sustain.
- Involve operators in cleaning and organizing their workstations.
- Standardize storage areas, tools, and procedures.
Step 6: Launch Autonomous Maintenance (Jishu Hozen)
Why it matters: Empowers operators to take ownership of daily equipment care.
How to do it:
- Train operators to perform basic maintenance tasks (cleaning, lubrication, inspections).
- Create checklists and schedules for daily checks.
- Encourage operators to identify abnormalities early and report them.
Benefits:
- Reduces minor stoppages
- Improves early fault detection
- Builds a sense of responsibility among staff
Step 7: Introduce Planned Maintenance
Why it matters: Scheduled maintenance minimizes equipment failures and extends lifespan.
How to do it:
- Use historical data to schedule preventive maintenance tasks.
- Implement condition-based monitoring where applicable.
- Track Mean Time Between Failures (MTBF) and Mean Time To Repair (MTTR).
Step 8: Focused Improvement (Kobetsu Kaizen)
Why it matters: TPM is about continuous improvement. Even small changes can have a big impact.
How to do it:
- Form improvement teams to target specific losses (e.g., changeover time, defects, idle time).
- Use tools like Root Cause Analysis, Pareto Analysis, and Fishbone Diagrams.
- Prioritize quick wins and build momentum for larger improvements.
Step 9: Expand TPM Across All Pillars
Once your pilot is successful, expand TPM organization-wide and integrate the remaining pillars:
- Quality Maintenance – Eliminate quality defects through better process and equipment control.
- Early Equipment Management – Design equipment with TPM principles in mind.
- Training and Education – Equip staff with the skills they need to maintain and improve systems.
- Safety, Health, and Environment (SHE) – Embed safety into every maintenance and operation task.
- Administrative TPM – Apply TPM principles to support and back-office functions for end-to-end efficiency.
Step 10: Measure and Celebrate Success
Why it matters: Measuring performance keeps your TPM journey on track and motivates your team.
How to do it:
- Track metrics like OEE, downtime, breakdowns, quality rates, and maintenance costs.
- Compare progress with baseline data from the pilot phase.
- Recognize and reward teams for improvements and innovations.
Final Thoughts from Unichrone
Implementing TPM is a journey that requires dedication, teamwork, and a structured approach. But the rewards—higher productivity, fewer breakdowns, improved quality, and empowered employees—are well worth the effort. At Unichrone, we’re committed to helping organizations adopt TPM through expert-led training, practical workshops, and internationally recognized certification programs.
Explore Unichrone’s TPM Training and Certification Programs to equip your team with the knowledge and tools to drive transformation from the ground up.